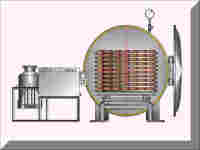
Итальянская фирма WDЕ с 1974 года производит вакуумные сушильные камеры в разных вариантах. Ее владелец Эрнесто Паньоцци — отец промышленной вакуумной сушки дерева (хотя первое упоминание о вакуумной камере было еще в 1854 году в Англии). Фирмы, которые делают вакуумные сушилки, пользуются его патентами.
Вакуумные камеры сушат в 8-10 раз быстрее обычных (а березу, например, в 14 раз) и очень эффективны при сушке толстых заготовок и ценных твердых пород дерева, склонных к образованию трещин в обычных камерах. Кроме того, они занимают меньше места и расходуют намного меньше тепла.
Сегодня многие фирмы производят вакуумные сушильные камеры. Но компания WDE по праву считается лидером в этой области: только семья Паньоцци (WDE в Италии и MASPEL в США) производят пресс-вакуумные сушилки. В этих камерах кроме вакуума с помощью специальной мембраны создается давление на штабель с усилием 10 000 кг/м2. Это позволяет применять более жесткие режимы сушки. Например, бук толщиной 32 мм сохнет в этих камерах до влажности 8% 29 часов, а сосна толщиной 25 мм — всего 17 часов! Объем камер от 0,3 м3 до 10 м3, что позволяет их использование на предприятиях с небольшим суточным объемом переработки.
Происхождение, сегодняшнее состояние и будущее вакуумных сушильных камер
1. Происхождение
Процесс вакуумной сушки древесины привлек внимание технологов в конце позапрошлого столетия. В патенте Ч. Говарда от 1883 года появляются первые попытки сушки древесины с помощью вакуума. В 1940 году к вакуумной технологии сушки обращается Войт, а в 1941 году опыты с автоклавом проводят Рихерс и Игни. В дальнейшем это работы Мэдисона (1956), Коллмана, Кришера и других. Опыты проводились как с постоянным, так и с дискретным вакуумом, но полученные результаты Вильером были оценены как «катастрофические», и проблема осталась нерешенной. В технологии сушения древесины вакуумом с применением конвекционного нагревания был сделан значительный шаг вперед Малквистом и Ноуком (1965). Все это так и остались на уровне лабораторных опытов.
Изучая промышленный и циклический вакуум (разрежение), Винченцо Паньоцци (доктор технических наук Туринского Политехнического Института, Италия) заинтересовался исследованием областей применения.
Стимулом явился растущий спрос деревообрабатывающей промышленности на сушку сырых пиломатериалов определенной толщины из твердых пород древесины, таких как бук, черная акация, дуб и некоторые очень твердые тропические породы.
2. Промышленные вакуумные сушилки.
С 1959 года по 1961 год Паньоцци проводил опыты по сушке небольших объемов древесины различных пород, используя вакуумный стеклянный колпак, в котором древесина нагревалась термоэлементами от утюгов.
Так родилась система «нагревательных пластин». Ее главным смыслом было использование высокой теплоотдачи при контакте древесины и пластин.
В 1962 году он построил экспериментальную сушилку диметром 800 мм с электрическими нагревательными пластинами, работающими в непрерывном вакууме, и с полезным объемом 0,5 м3.
В 1966 году он построил полупромышленный цилиндрический агрегат для пиломатериалов нормальных размеров с пластинами, нагреваемыми горячей водой, которые могли работать как в непрерывном, так и в циклическом вакууме.
1966 год может считаться годом рождения процесса промышленной вакуумной сушки (или «разрежение»), потому что с этой даты в промышленной практике начинается все более широкое применение этих сушильных камер.
В 1973 году по итогам пятой конференции в Южной Африке Сивидини представил первый официальный отчет Итальянского НИИ древесины по исследованиям в области сушения.
Вскоре стало ясно, что так называемый «метод пластин» не имеет будущего. Еще в шестидесятых годах «вакуумный метод» часто отвергался как очень трудоемкий и неэкономичный процесс, потому что он требовал значительных инвестиций в оборудование, а ручное управление нагревательными пластинами было очень трудоемким.
В 1975 году, после проведения исчерпывающих исследований, Винченцо Паньоцци построил и показал в Ганновере вакуумную сушилку с нагревом горячим воздухом. Это был цилиндрический агрегат известный под маркой BS, имеющий максимально полезную длину 12 м и внутренний диаметр 2,3 м. Каждая такая секция может вмещать 24 м3 древесины.
Характеристикой этого агрегата была конвекционная нагревательная система с вентиляцией, перпендикулярной по отношению к штабелю: поток воздуха, нагретый на внутренней цилиндрической стенке, перемещается мобильным соплом; под воздействием вращения этого сопла древесина подвергается нагреву с мощными турбулентными пульсациями с периодической сменой вакуумными фазами.
С тех пор вступил в силу патент Маспелла, основанный на циклическом процессе с «нормальным пресс-нагревом» и «вакуумной сушкой» (Маспелл — это компания, основанная Паньоцци).
Промышленные сушилки этого типа нашли распространение в производстве, работающем с толстым и трудно сушимым пиломатериалом. Простая полуавтоматическая система позволяла управлять процессом сушения. В дальнейшем, объединение двух одинарных сушилок в единый агрегат «Тандем» дало заметное сокращение энергозатрат.
3. Дальнейшее развитие вакуумного процесса.
В 1986 году появилась система LO-LA (продольно-горизонтальная) с вентиляторами (минимум двумя), которые были помещены в цилиндрические цоколи и создавали два встречных воздушных потока. Направление движения потоков изменялось механическим способом или электрическим с помощью инвертора с тем, чтобы образовать единый перпендикулярный по отношению к штабелю воздушный поток, который ежеминутно двигался вперед и назад вдоль штабеля.
Этот тип вентиляции LO-LA имеет следующие преимущества:
— уменьшение количества вентиляторов;
— снижение энергопотребления;
— рост аэродинамической отдачи;
— увеличение скорости прохождения воздуха через штабель;
— исключение застоя воздуха в точках наименьшего сопротивления;
— несложность установки моторов внутри камеры для превращения механической энергии в тепло.
В системе LO-LA чередование периодов в циклическом вакууме применяется, когда древесина имеет повышенную влажность или необходима сушка высшего качества, а непрерывный вакуумный процесс применяется, когда не требуется высокого качества сушки или древесина уже предварительно подсушена.
Первоначально сушильные камеры изготавливались из углеродистой стали, поэтому цилиндрическая стенка камеры и крышки подвергались нагреванию как для того, чтобы нагреть древесину, так и чтобы избежать конденсации воды на стенке, что могло привести к коррозии.
К этой активной защите от коррозии была добавлена пассивная защита. Для этого внутренние стенки камеры зачищались и покрывались слоем эпоксидной смолы.
Тем не менее, полностью эту проблему решить не удалось и каждые 3-4 года приходилось обновлять слой смолы. Коррозия вообще является одной из основных проблем при эксплуатации всех типов сушильных камер и чтобы радикально решить эту проблему, с 1990 года Маспелл изготавливает все контактирующие с влагой части сушильных камер из нержавеющей стали. Нужно отметить, что Маспелл нашел способ уменьшить вес (и стоимость) нержавеющих частей сушилок. Камера имеет двойную стенку: наружная изготавливается из обычной стали и имеет толщину достаточную, чтобы выдержать наружное давление, а внутренняя стенка изготавливается из тонкой нержавеющей пластины (толщина 1-2 мм), которая не может выдержать внутреннее разрежение. Чтобы компенсировать внутреннее разрежение и превратить его в давление, между стенками камеры создается сильный вакуум, поэтому внутренняя стенка подвергается давлению по направлению изнутри наружу. Кроме того, этот слой сильного вакуума является наилучшим термоизоляционным барьером и препятствует потерям энергии.
Следующим шагом вперед был переход от цилиндрической формы камеры к параллелепипедной, поскольку цилиндрическая форма является препятствием для строительства сушильных камер больших объемов. Началом этого стало создание сушилки типа «Тетра» с прямоугольной секцией, вмещающей штабель 1,2м*1,2м*12м.
Успех сушилок Тетра привел к еще более дерзкому шагу: был создан гигантский «Голиаф». Самая последняя сушилка Голиаф, наконец, позволила Маспеллу достичь цели производства вакуумных сушильных способных вмещать сразу полный грузовик заготовок, так как размеры загрузки составили 2,5м*2,5(3)м и полезной длиной 13,6м и даже больше.
Внешний диаметр аналогичной цилиндрической сушильной камеры, вмещающей не только этот штабель, но и систему вентиляции, достигал бы 4м и, в этом случае, ее транспортировка стала бы проблематичной, поскольку ее параметры превышают разрешенные транспортные размеры.
Таким образом, Голиаф, сочетая продольно-горизонтальную систему вентиляции моделей LO-LA с последовательной инжекторной нагревательной системой с вертикально перемещаемым отражателем, решил проблему сохранения размеров в рамках транспортных ограничений, попутно улучшив аэродинамику системы вентиляции. В днище и двери Голиафа расположены два ряда вентиляторов по три в каждом ряду и водно-воздушные теплообменники. Вертикальные подвижные отражатели, совершающие однообразные перемещения от одного конца камеры к другому, обеспечивают однородность воздушного потока.
Вакуумная сушилка типа Голиаф может работать как в непрерывном, так и в циклическом вакууме. Обычно она работает в циклическом вакууме, в котором возврат теплоэнергии достигается объединением двух камер, что чрезвычайно снижает стоимость сушения до нижнего предела затрат при использовании конвекционных сушилок.
В феврале 1992 года во Франции на лесопильном заводе Трюшо был установлен первый агрегат Тандем Голиаф 100.
E.D.F. (Французские электросети), которая финансировала проект, приняла решение поручить S.F.E.E. и С.Т.В.(Технический Центр в Боа) замеры, чтобы подтвердить затраты, качество и затраты времени этого агрегата. Официальные результаты должны быть опубликованы, но мы можем отметить, что в первых двух тестах при сушке в «тандеме» дубовой доски толщиной 27 мм со средней начальной внутренней влажностью 23,5% и конечной влажностью 10,2%, затраты тепловой энергии бойлера составили 0,4 кВт/кгН2О, а при сушке только одной камерой без возврата теплоэнергии, затраты составили 0,869 кВт/кгН2О.
В общем, основываясь на анализе вышеупомянутых результатах и ранее проведенных исследованиях, можно утверждать следующее:
— сушилки типа Голиаф — это агрегат большой производительности удобный для обработки больших размеров;
— поскольку он вмещает полный грузовик древесины, Голиаф соответствует нуждам компаний, которые используют для перевозки древесины грузовики;
— значительно сокращая время сушки по сравнению с обычной сушилкой, Голиаф позволяет существенно уменьшить количество древесины на складе и быстро реагировать на запросы рынка;
— существенное снижение расходов понижает стоимость сушения;
— что касается периода амортизации, сушилка может работать гораздо более длительное время, поскольку камера из нержавеющей стали очень долговечна, и, следовательно, приносит дополнительную прибыль до истечения срока амортизации;
— по причине долговечности Голиаф сохраняет высокую рыночную стоимость и к концу периода амортизации имеет оптимальную остаточную стоимость.
4. Пресс-вакуумные сушильные камеры и их развитие.
Макспелл никогда полностью не отказывался от принципа нагревания пластинами, который очень эффективен с точки зрения передачи тепла. Он применил этот принцип в новой и оригинальной пресс — вакуумной сушилке. А вообще практическое применение пресс-вакуумной сушки началось в 1985 году.
Сушильная камера представляет собой резервуар из нержавеющей стали в форме параллелепипеда с крышкой, которая состоит из резинового листа закрепленного в жесткой раме. Она открывается таким образом, что позволяет осуществить загрузку древесины сверху. Внутрь камеры древесина загружается вручную, и каждый слой прокладывается нагревательными пластинами.
В процессе сушки под воздействием вакуума, производимого помпой, резиновый лист прижимается к верхней нагревательной пластине и давит на штабель с усилием порядка 100 кПа. Это давление присутствует все время сушки и заставляет древесину выпрямляться, даже если первоначально она была искривлена.
В пресс-вакуумной сушилке применяется система (регенерации) возврата энергии путем конденсации одним из преобразователей водяного пара, извлеченного из древесины после того, как его температура повысилась с помощью компрессии, создаваемой вакуумной помпой. Возврат энергии возможен также от горячего масла помпы, так как применяемая помпа — это вакуумная масляная кольцевая помпа. Таким образом, без применения бойлера можно получить количество тепла, почти достаточного для обеспечения всего процесса после первого этапа нагревания.
Скорость сушки практически такая же, как и при использовании обычных сушилок с применением высоких температур, но здесь температура вдвое меньше и, поэтому, цвет древесины не меняется. Самая маленькая пресс — вакуумная сушилка «Микро» вмещает 0,6 м3 пиломатериалов. Ее внутренние размеры: 800х5000х140 мм.
Для увеличения вместимости и облегчения загрузки, был разработан новый тип сушилки — «Мега». Ее внешние размеры: длина — 5,5 м, ширина — 1,8 м, высота — 1,8 м. Вместимость — около 5 м3 с использованием различного количества (в зависимости от толщины пиломатериала) нагревательных пластин. Эта сушилка, в отличие от других пресс — сушилок, снабжена загрузочной тележкой на рельсах и дверью для загрузки-выгрузки. Древесина и пластины загружаются с помощью подъемника на присосках. Эта система исключает физическую работу персонала и значительно сокращает время загрузки/выгрузки. Возможно также применение других способов загрузки.
Применение некоторых моделей пресс-сушилок исключительно интересно в ремесленном и малом бизнесе тем, что полностью отвечает требованиям рынка: сравнительно низкая цена покупки, простота условий сушки, высокая производительность, несмотря на ограниченный объем загрузки. Данная сушильная камера может работать и с автономным электрическим бойлером. Ее
нужно только подсоединить к электрической сети, системе водоснабжения и к воздушному компрессору.
5. Перспективы.
Поскольку вакуумный принцип сушки ограничен областями применения, например, при сушении толстых заготовок из твердых пород древесины с высокой первоначальной влажностью, или в ремесленном и малом бизнесе. В настоящее время ситуация меняется, потому что значительность получаемых результатов о преимуществах данной системы все более или более убедительна.
Более того, с появлением на рынке модели Голиаф область применения существенно расширилась за счет крупного производства, причем как лесопильного, так и производящего готовые изделия. Поэтому можно предположить, что в ближайшем будущем большая часть мирового рынка, связанная с крупным производством (а это по последним данным 30-40%), будет нуждаться в прямоугольных вакуумных сушилках типа Тетра и Голиаф. А пресс-вакуумные сушилки, предназначенные для ремесленного и малого бизнеса, будут распространяться спонтанно благодаря удивительным способностям: скорость и высокое качество сушки и простота обслуживания камеры.
Более того, по идее, предложенной некоторое время назад IUFRO, вакуумный сушильный процесс принципиально дает возможность получать прибыль при «смеси пород и целей». Действительно, вакуумные сушильные камеры способны не только значительно сократить время сушения, но и нивелировать процесс сушения для разных пород древесины и заготовок разной толщины.
Для Маспелла, выдвигающего и патентующего идеи, характерны следующие утверждения:
— оптимизация качества сушения;
— простота производственных структур для управления и автоматизации;
— максимальное снижение эксплуатационных расходов с целью сделать вакуумную сушильную камеру более выгодной по сравнению с другими системами.
Все это гармонирует с целями IUFRO и со склонностью Маспелла к сотрудничеству со всеми институтами IUFRO для достижения этих целей.